Do my products require on-site testing
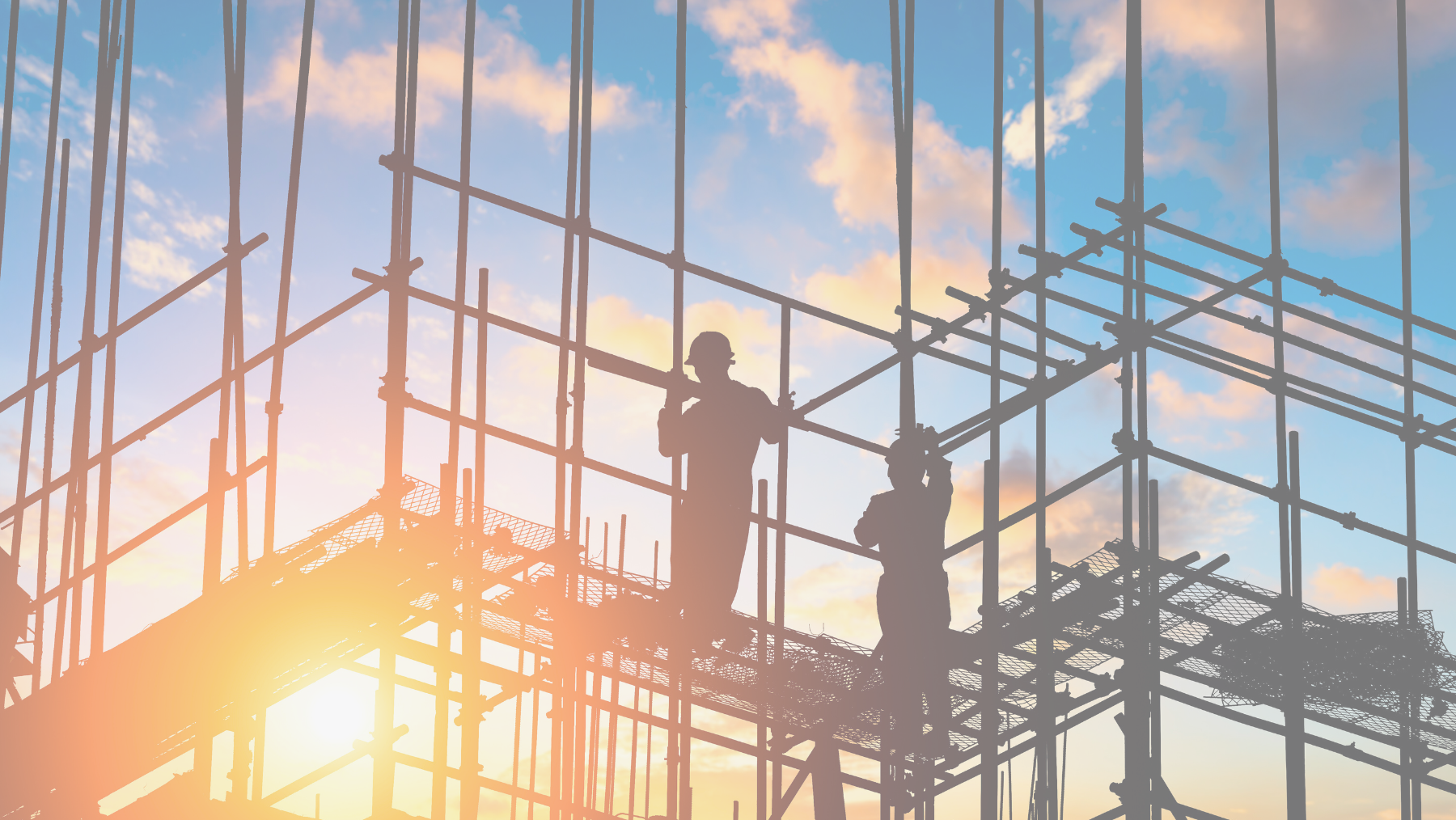
On any construction site, it’s vital that the equipment you’re using is fit for purpose.
For one thing, there’s the wellbeing of the users to ensure, both on-site and during installation. If equipment is being brought onto the site, you have to know that the team handling it will be safe. Then, there’s the product's end user and service life to consider, for the project's overall success.
Without sufficient assurance of a product’s quality, there are significant issues surrounding accountability. If something goes wrong – if a piece of equipment fails to work – it’s likely to be the subject of an investigation. Questions will be asked about whether the installation is to blame or the product itself. By ensuring the equipment you’re using is appropriately tested, much of that potential concern can be eliminated.
Given the importance of this, you might assume that all equipment should be tested on-site before use. But in reality, that isn’t so. At CFS, we offer two main types of products: lifting and fixing.
And in the majority of cases, they will be ready to use upon arrival.
The question, therefore, is how can you tell if a product requires on-site testing?
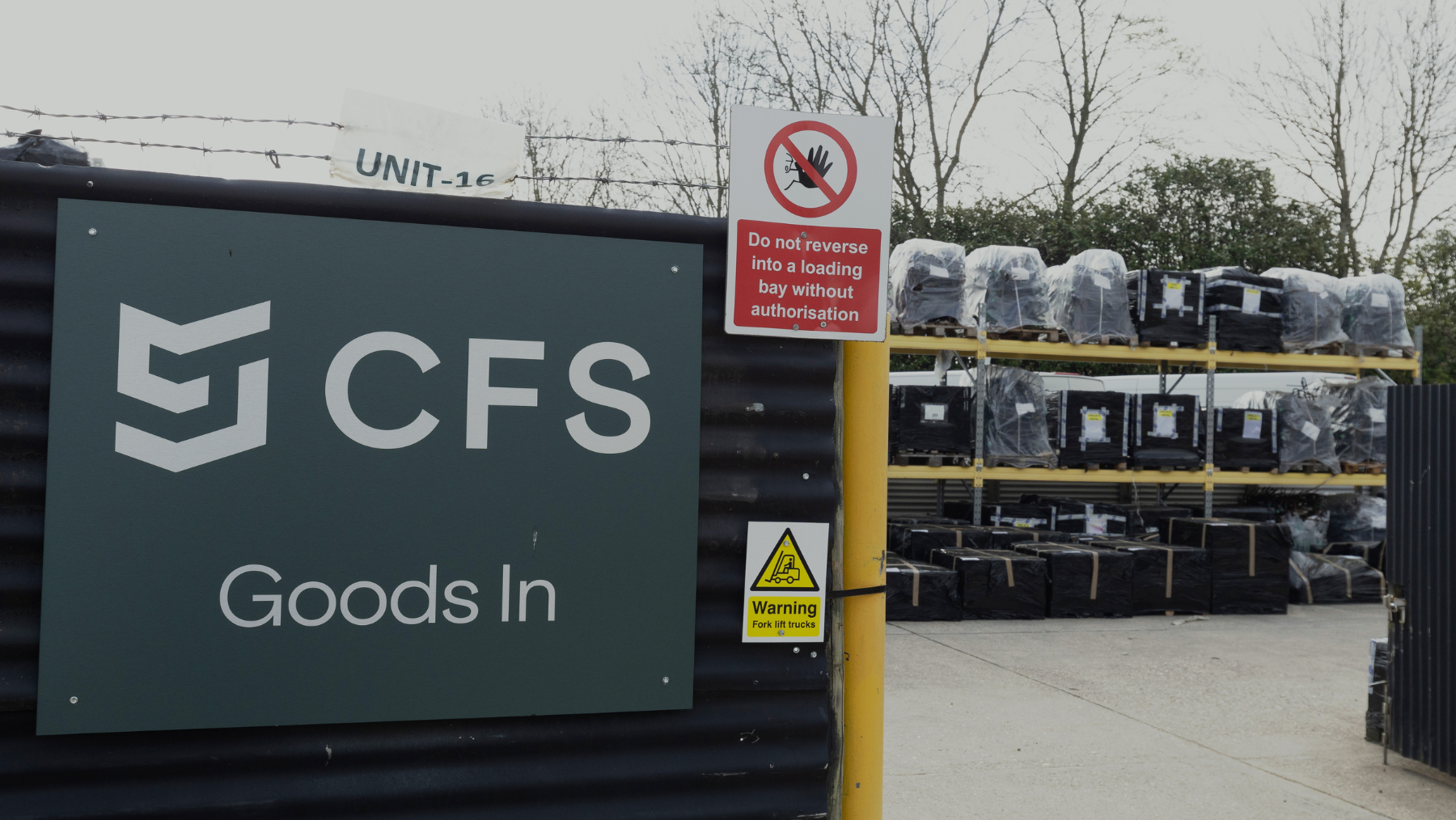
55%
When is on-site testing required?
Generally speaking, lifting applications will only require on-site testing in the event of some sort of user error, such as with the manufacturing process.
Take cast-in sockets, for instance. They’re put into a concrete mould and left to cure for twenty-four hours, before being removed from the moulds and then transported to site. They have standard applications, and we provide support to ensure they’re adequately designed for the required use. With that in mind, the only time they should require on-site testing is if there’s an obvious error with the installation or perhaps some cracking is observed around the lifter.
Fixing, in some ways, is more straightforward.
A significant number of the fixing solutions we offer at CFS are covered by an ETA certificate (European Technical Assessment). This provides certification of an independent, Europe-wide procedure for assessing the essential performance characteristics of fixing products, and applies when the products aren’t fully covered by a harmonised standard under the Construction Product Regulation (EU) 3052011.
ETA approval is crucial, for the sole reason that, according to the CFA (Construction Fixing Association), where a product is being used within the parameters of an ETA, there is no requirement to perform further testing on site. With that in mind, familiarising yourself with this process and learning to identify products that have ETA certificates can save a huge amount of time and resources.
ETA certificate (European Technical Assessment) provides certification of an independent, Europe-wide procedure for assessing the essential performance characteristics of fixing products
Can these products be tested anyway?
On occasion, site managers will be asked to test a product which, strictly speaking, doesn’t need it. There might be other parties involved that overlook the ETA approval, asking for further testing either to satisfy their own criteria or because they aren’t confident in how something’s been installed. In some cases, they might not actually realise that with an ETA, further testing isn’t needed.
At best, this can simply present an extra hoop to jump through. At worst, however, it’s a waste of time and money. As a result, where products with an ETA have been installed by competent individuals, and there is no requirement to test, sites should avoid this unnecessary step wherever possible. Being aware of which products require testing – and, crucially, which don’t – is a sure-fire way of ensuring a site is as efficient and compliant as possible.
CFS products with ETA approvals include MBA cast-in channels, PEC cast-in channels and stud anchor sockets.